A global sustainability leader
Delivering stronger, smarter, happier neighbourhoods
Creating a better way to live.
At Frasers Property Australia, social and environmental sustainability is integral to our ambition to create stronger, smarter, happier neighbourhoods that promise greater futures. From site acquisition and project design to delivery, operation, reporting and beyond, we’re guided by a sustainability strategy that reduces our impact on the planet, while improving quality of life for people.
Through fostering resilient communities, carbon-reducing initiatives, responsibly sourcing services and materials, providing clean energy, using green finance and being accountable through independent tools and ratings, we contribute to a better, cleaner future.
Our Priorities
Sustainability priorities evolve constantly. As such, we need to be flexible and resilient. We need to rethink our current systems and technologies to enable sustainable development and to make a difference in a changing world.
We're fostering an innovation culture to develop scalable solutions, and to create adaptable places that will withstand shifts in demographics, climate and lifestyle.
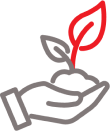
Energy & Carbon
We are committed to reducing our carbon footprint in line with the SBTi 1.5°C pathway and future-proofing our properties and communities.
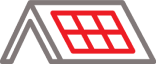
Climate Resilience
Frasers Property Australia is committed to building healthy, resilient communities for today and the future. Our ESG strategy ensures assets are climate-resilient and maintain healthy living conditions during extreme weather.
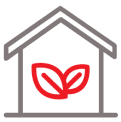
Integrated Nature
By seamless integration of nature into our development process, we enhance site ecology, reconnect people with nature, and contribute towards improving indoor and outdoor quality.
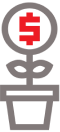
Responsible Investment and Certification
We validate our initiatives through appropriate certifications and maintain ongoing reporting commitments. We also include environmental, social and governance considerations in all investment proposals.

Materials & Supply Chain
We realise our impact extends beyond our operations to our supply chain. It’s why we are on a mission to source safe and responsible materials and we are working with our supply chain to make this a reality

Efficient use of water and waste management
We build properties and communities focused on minimising resource use and landfill waste. We install efficient water fixtures, promote rainwater capture and/or recycled water use, and implement waste management plans that are monitored monthly.

Health and Wellbeing
We ensure thermal comfort and indoor air quality through selection of building materials, ventilation systems and both passive and active building systems to create healthy and thriving spaces. Our resilience and integrated nature considerations also strengthen our health and wellbeing strategy.
Happier communities
Our purpose as a business is to create belonging. This begins with the way we expertly design our neighbourhoods, and continues with the support we give to communities as they form and grow.
In addition to our investments in community development, Frasers Property Australia is engaged in a mission to raise awareness and reduce the impact of loneliness in Australian life. In this fight, we are very proud to be a producing partner in the documentary film, The Great Separation, and an industry advisor to Ending Loneliness Together.
Smarter environments
Finding better ways to live with lower impact has been our focus for decades. We’ve led the way with innovations that have improved the energy and water use of homes including Green Star design, geothermal and solar energy capture, and carbon-neutral power supply through our energy retailer, Real Utilities.
World leadership
We were the first in the world to achieve Living Building Challenge® Petal Certification for a retail building, and in doing so, we developed The Greensheet, Australia’s first comprehensive database of healthy building materials, freely available for everyone’s use. Additionally, 100% of our corporate funding is secured in the form of sustainability-linked loans.
Resilient communities
Thirteen Frasers Property communities are certified under the Green Star Communities tool, seven of which have achieved a 6 Star rating, representing World Leadership in sustainability. The remaining six have certified 5 Star ratings, representing Australian Leadership. We’ve also maintained the highest possible GRESB 5-star rating since 2018.
Real Utilities
Real Utilities is Frasers Property Australia’s carbon-neutral energy retailer providing 100% Climate Active-certified energy to many of our residential, commercial, and mixed-use developments. It plays a key role in both our decarbonisation efforts and those of our customers.
Strong foundations
World leadership
We have maintained the highest GRESB 5-star rating since 2018.
Our sustainability approach, from our carbon-reducing initiatives, use of green finance, increasing the resilience of our communities, responsibly sourcing services and materials, and using third-party certifications to benchmark our work, underpins our global leadership position.
Resilient communities
Thirteen Frasers Property communities are certified under the Green Star Communities tool and seven have achieved a 6 Star rating, representing World Leadership in sustainability.
The remaining six have certified 5 Star ratings, representing Australian Leadership.
Organisations
An award-winning approach
Our pioneering projects and initiatives set new standards and improve sustainability results industry-wide. As a global sustainability leader, we’re consistently recognised for our achievements across various sectors and regions, as well as on multiple award platforms.
OVERALL WINNER
Burwood Brickworks
Living Building Challenge, Sustainability Leaders 2022
SHORTLIST
Real Utilities
Sustainability Leaders 2022
WINNER
Burwood Brickworks
Best Sustainable Development – New Buildings, Property Council Innovation & Excellence Awards 2021
FINALIST
Ed.Square
Sustainability & Environmental Technology, UDIA NSW Awards for Excellence 2021
SHORTLIST
Burwood Brickworks Shopping Centre
Sustainable Architecture, Victorian Architecture Awards 2021
WINNER
Central Park Sydney
Excellence in Sustainability, Urban Developer Awards 2019
WINNER
Central Park Sydney
Excellence in Sustainability & Environmental Technology, UDIA NSW Awards for Excellence 2019
FINALIST
Frasers Property Australia
Business Leadership in Sustainability, World Green Building Council Asia Pacific Awards 2018
WINNER
Central Park Sydney
Sustainable Architecture, AIA National Architecture Awards 2017
WINNER
Fairwater Park
Sustainability Award, Green Globe Awards 2016
HIGHLY COMMENDED
The Ponds Shopping Centre
Built Environment Sustainability, Green Globe Awards 2015
GOLD MEDAL
The Ponds Shopping Centre
Sustainable Design, ICSC Asia Pacific Shopping Centre Awards 2015
WINNER
Discovery Point
Sustainable Development, UDIA NSW Awards for Excellence 2015
WINNER
One Central Park
Best Sustainable Development of the Year, LEAF Awards 2014
Find your stronger, smarter, happier neighbourhood today